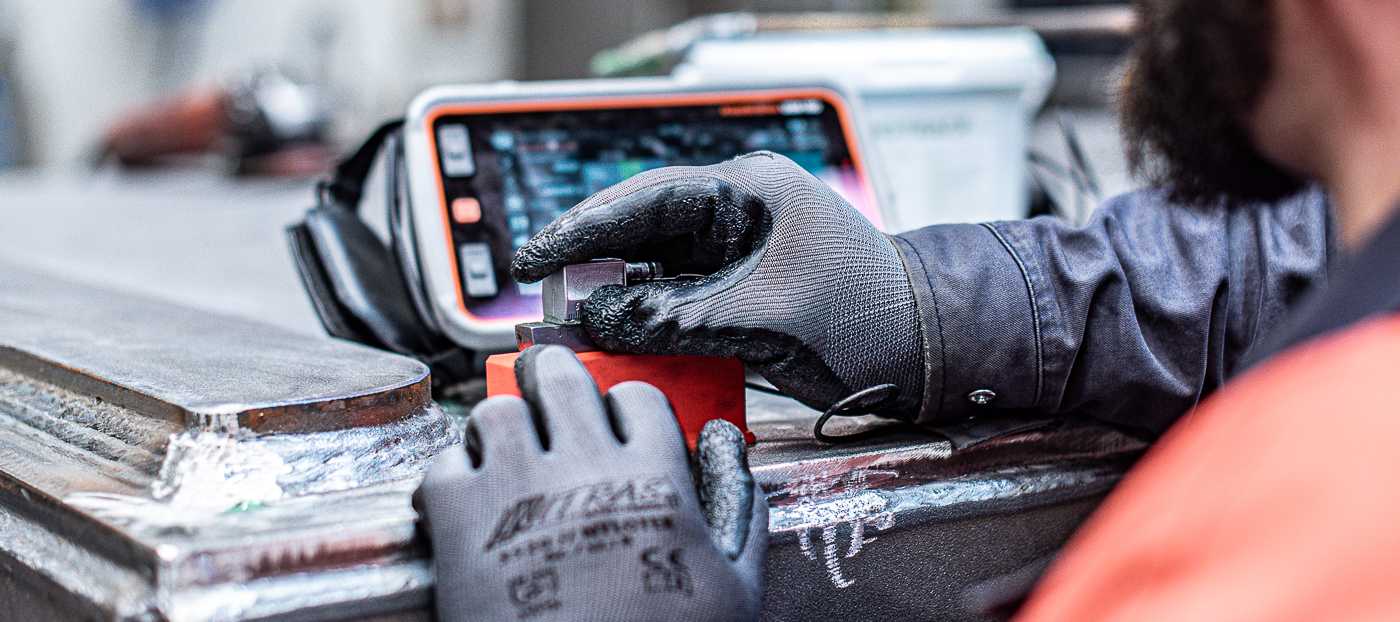
Technologies
We offer customized solutions that are perfectly tailored to your requirements. From precise flame cutting to skilled welding and annealing - we ensure that your steel project is successfully delivered.
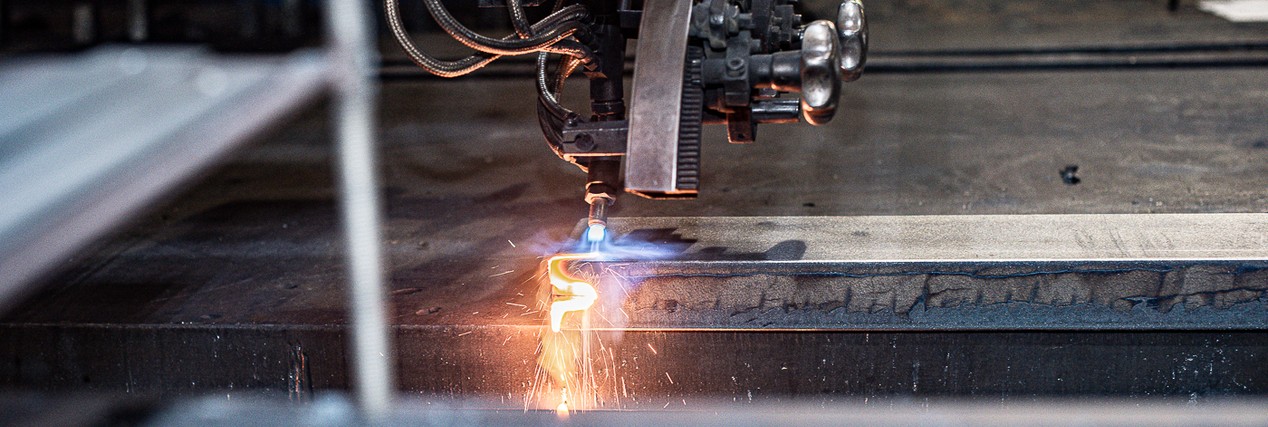
Autogenous cutting and plasma cutting
Our signature disciplines are autogenous cutting and plasma cutting. We are able to cut with up to 8 torches in parallel and on several levels.
We can handle thickness ranges from 8 to 1,100 mm, widths of up to 6,600 mm, lengths of up to 20,000 mm and piece weights of up to 55 tons.
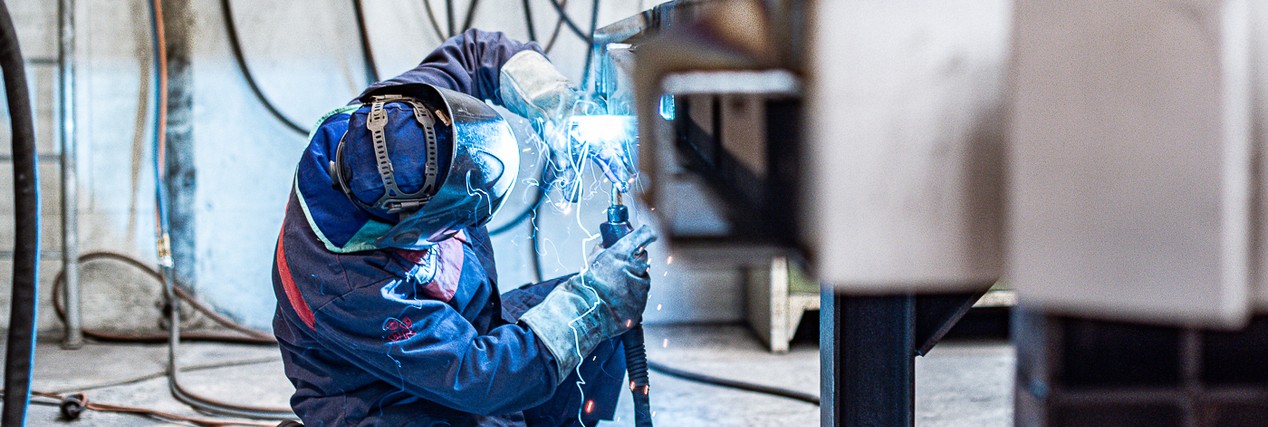
Welding
We have developed into an efficient system provider for the production of ready-to-install welded components with unit weights of up to 160 tons.
- Welding of fine-grained structural steels too
- Welding / hardfacing of cast iron
Our certifications:
- ISO 3834-2:2021 sowie nach
- EN 1090 Exc 4
- DIN 2303 (military technical approval)
MIG/MAG/UP welding systems
Rotary tilting welding table: for 35 t unit weight
2 welding robots:
Factory 1:
x-axis max. 5,500 mm
y-axis max. 3.700 mm
z-axis max. 3.000 mm
Factory 2:
x-axis max. 15.500mm
y-axis max. 6.000 mm
z-axis max. 5.500 mm
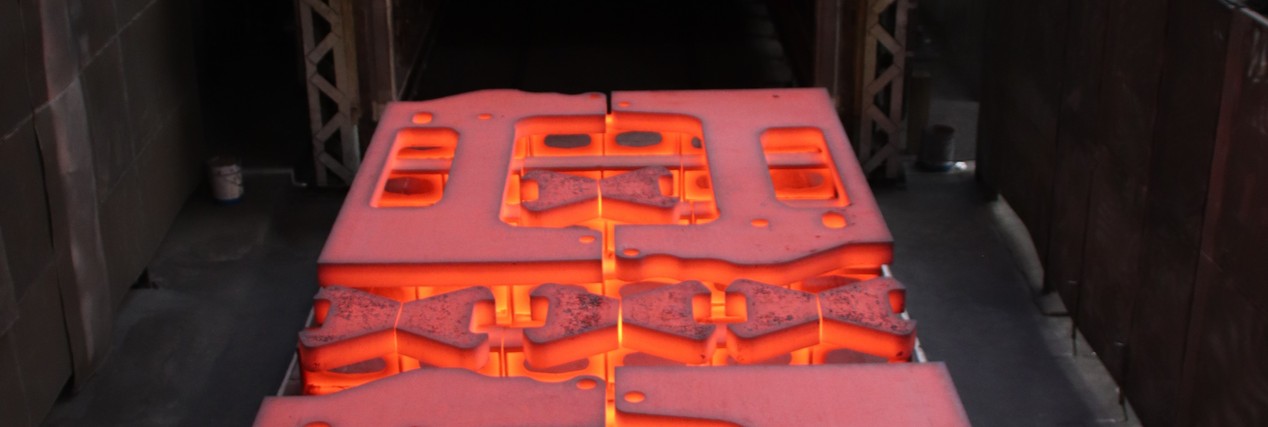
Annealing and vibration stress-relieving
Through established and innovative technologies such as low-stress annealing or vibration stress relieving, we are able to reduce stress even in large welded components.
By annealing in our production facility in Korntal, we can treat parts weighing up to 40 tons. We are also able to cover additional weights through our partner network.
Vibration stress-relieving offers the possibility of stress-relieving parts from a unit weight of just one ton. This service is mobile and can therefore be used both in our production facilities and on your premises.
We are working on innovative solutions and continue to test them in our production and in cooperation with customers.
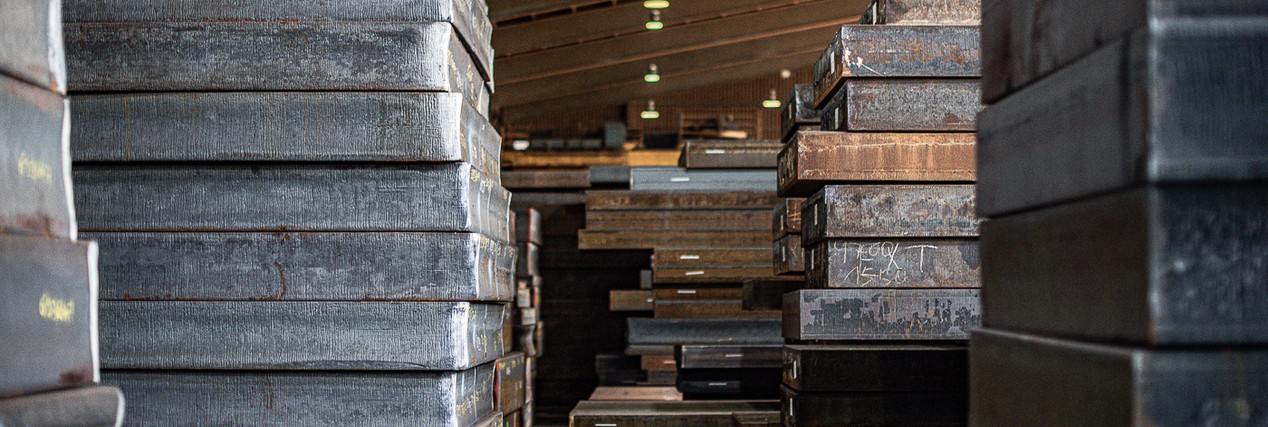
Straightening
Straightening press: according to DIN or customer requirements with up to 3,500 kN pressureRichtpresse: nach DIN oder nach Kundenwunsch mit bis zu 3.500 kN Druck
Flame straightening: specific straightening of thick sheets
Flame straightening uses flame to heat the steel locally to bring it into the desired shape. This method is often used for thick steel components where fast and precise straightening is required.
An oxyfuel torch is used to create a concentrated heat area. Through targeted heating and cooling, the steel can be bent or straightened. It requires experience and expertise to achieve the right temperature and angle without damaging the steel. The temperature ranges between 550 and 700 ° Celsius.
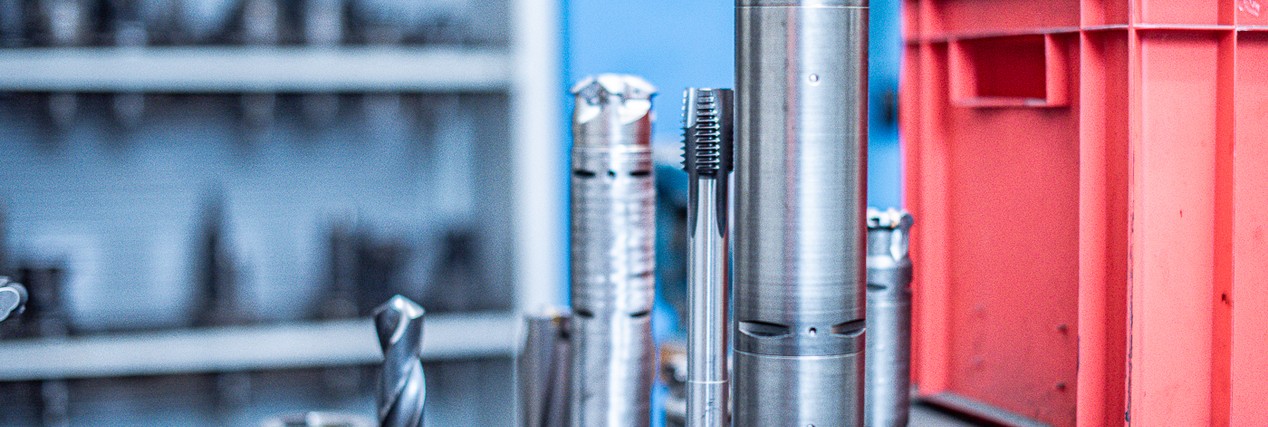
Mechanical processing
We also provide the finishing touches to large components manufactured with millimeter precision.
Our maximum sizes are 7,000 mm in the x-axis, 2,900 mm in the y-axis and 1,300 mm in the z-axis and a maximum unit weight of 16 tons.
We rely on a strong partner network for further processing and larger machining dimensions.
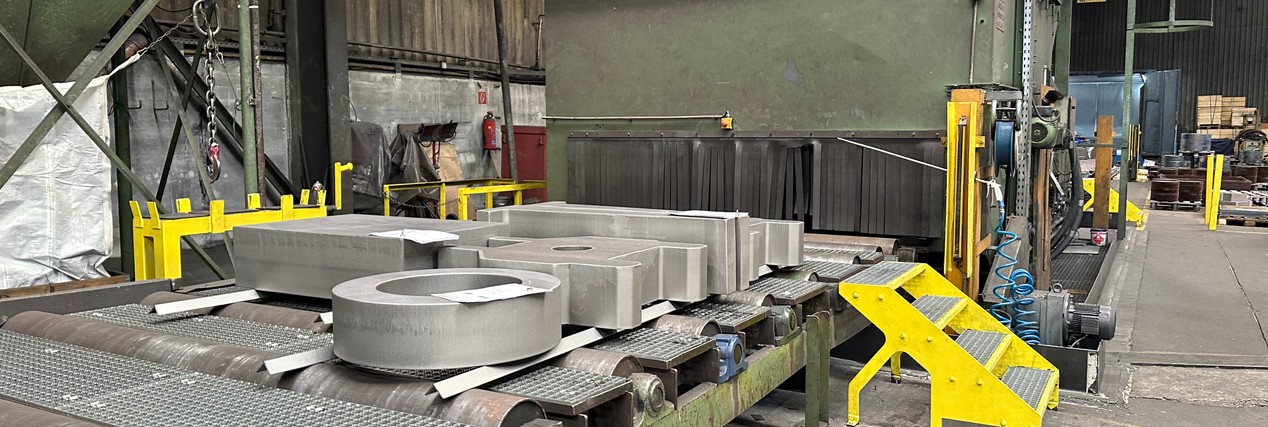
Sandblasting, priming and painting
We also offer surface treatment by sandblasting, the application of a primer to improve adhesion and corrosion protection and final painting to refine and protect your surfaces.
Continuous blasting system:
width up to 2,700 mm // specify height
Blast cabinetcolon;
Filling weight plant 1 max. 40 t
Filling weight plant 2 max. 160 t
2 spray booths:
Factory 1 for solvent and water-based paints
Width 5.000 mm
Length 9.000 mm
Height 2.500 mm
Unit weight max. 40 t
1 paint booth:
Factory 2 for solvent-based paints
Width 5.800 mm
Length 11.500 mm
Height 3.800 mm
Unit weight max. 160 t
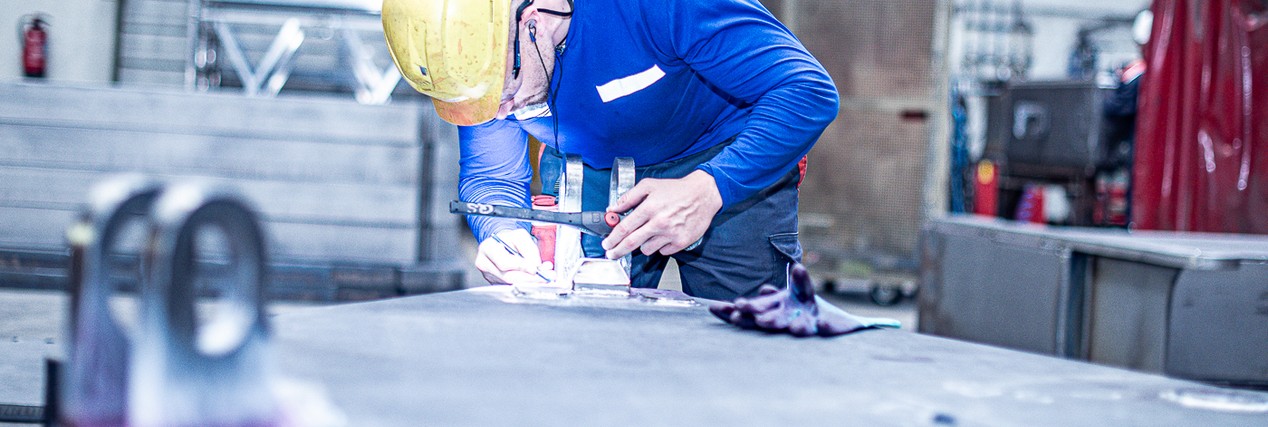
Quality management and assurance
Our ISO 9001:2015 certification guarantees consistent quality controls along the entire process chain. All our quality inspectors are certified according to DIN EN ISO 9712 in the respective process.
Our testing options:
- Ultrasonic testing according to customer specification or standard
- Penetrant testing (red-white or fluorescent)
- Magnetic particle testing (black and white or fluorescent)
- Visual inspection of weld seams
- Surface roughness testing
- Spectral analysis
- Hardness testing
- Component inspection using augmented reality (SuPAR)
- 3D measurement using Faro Tracer (registered sign)
➝ All testing options with corresponding documentation are available from us if required
Special tests such as phased array technology for fast and reliable testing are provided by our partners.
Let's get in touch
Personal contact is essential. We look forward to your inquiry and challenges, for which we are sure to find the perfect solution together with you.
Tel.: +49 (0) 711 80 02-0
Email: info@jebens.dillinger.biz
Daimlerstraße 35–37 D-70825 Korntal-Münchingen Germany